VARTECH Technology: An Unbelievably Easy Method That Works for Your Gas Turbine
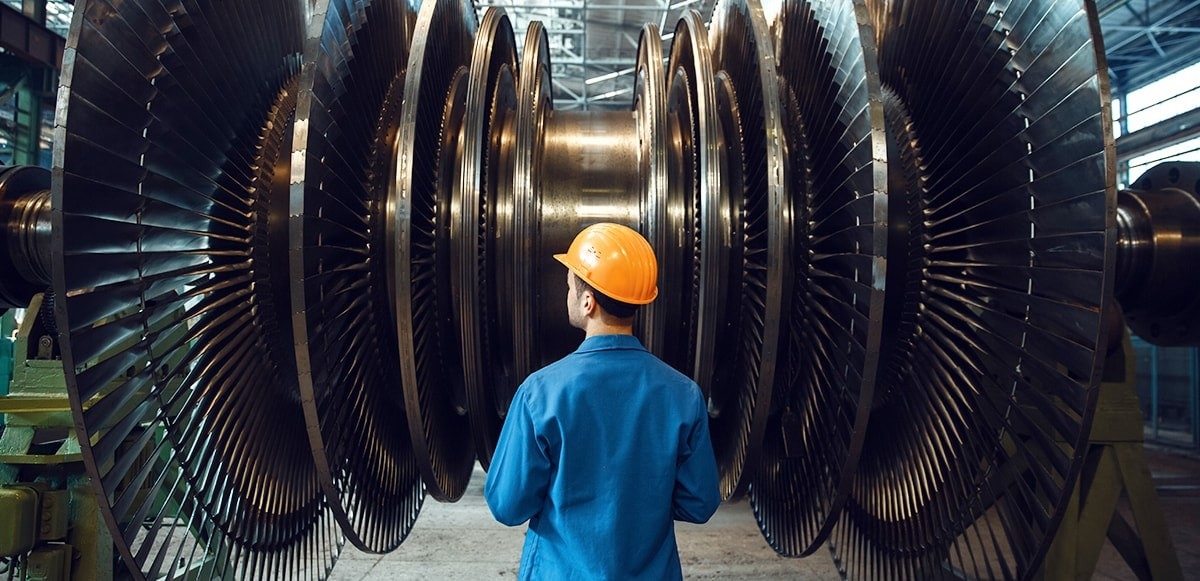
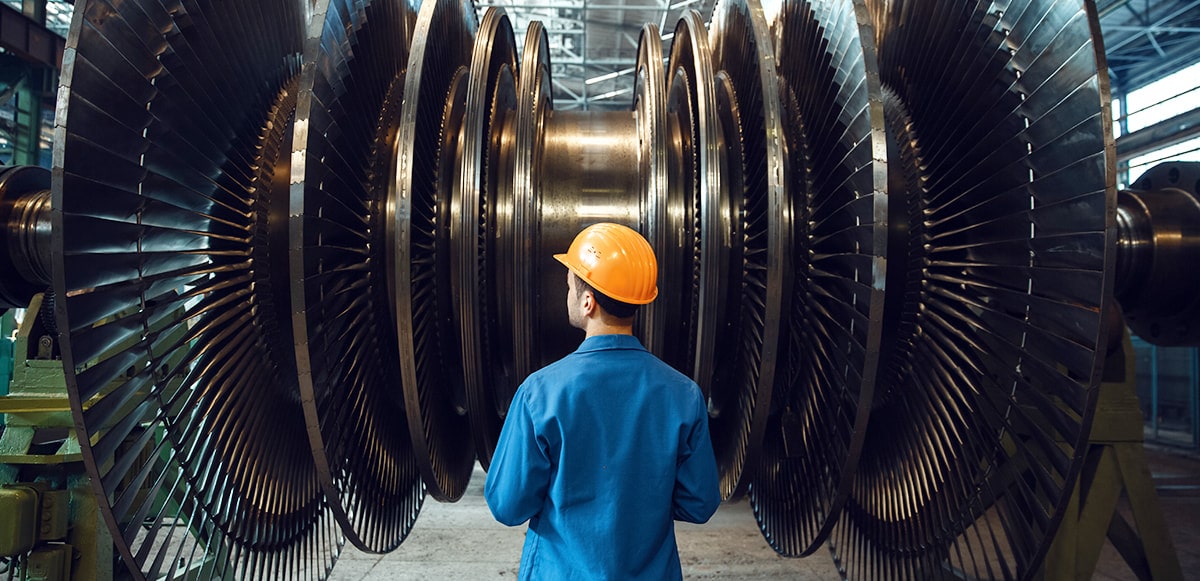
To understand how VARTECH Technology can work incredibly well for your Gas Turbine, it is important to understand varnish and the problem it creates.
Varnish is a broad term covering various kinds of deposits in oil systems. Some types are rigid and firm, others sticky, and others are commonly referred to as sludge. However, the common factor is that they typically begin from the degradation of the oil in the system.
Varnish usually forms and sticks in areas that are extremely hot or very cool and sluggish.
Now, measuring or finding varnish is an enormous challenge since varnish does not turn up in the oil, but on the metal surfaces. The only way to identify varnish is to see it on a surface or to experience its effect. For example, a sticky valve is an apt indicator of the presence of varnish.
It is triggered in many ways. The cycle of varnish begins with something that upsets the lubricant’s stability, such as excessive heat. This can lead to the degradation of the oil, resulting in the formation of impurities. For a while, these impurities often remain dissolved in the oil, causing no harm. But, as more and more accrue, however, they stick together, forming insoluble, suspended submicron particles and once they stick to metal surfaces, they become varnish.
Varnish accumulation reduces a lubricant’s heat transfer properties and causes your system to run hotter and hotter. The consequences won’t just jeopardise your equipment — it will cause de-rated equipment, unpredicted shutdowns, inefficient operation, enhanced maintenance labor management, and spending, higher costs, and lost profits for the owner.
In some turbines, varnish focuses on servo valves, causing them to stick and either delay movement or refuse to move, which can send the turbine out of operation, causing a complete shutdown. In a peaking turbine, one that is held in reserve for peak demand, stuck servo valves can lead to failure to start. Downtime and repair costs can run anywhere from $100,000 into the millions.
Varnish buildup in gas turbines is a big concern for our industrial lubricant customers. While some cleaners in the market are effective in certain circumstances, they may also present several issues. But, VARTECH Technology has addressed the issues of greatest concern, namely water separability; oxidation stability; and seal compatibility.
Residual dispersal/detergent cleaner remaining in the oil system when the oil is changed can ruin the fresh oil that is installed. To ensure that the cleaner is expunged from the system, a full flush is required.
This is where VARTECH™ Industrial System Cleaner (ISC), can come into play. A non-solvent-based solution that can be added straight to oil during operation, VARTECH technology cleans varnish and sludge from the system before a regular oil change. In exhaustive lab testing against existing products, Chevron VARTECH™ ISC showed very good seal compatibility, water/oil separability, and oxidation performance.
To understand how VARTECH Technology can be an incredibly easy method that works for your gas turbine, we can take a case in point of offshore production platforms with three turbines on board. The turbine in question had a severe varnish issue and the oil cooler had been contaminated, rendering the temperature rise to where the operators would have to shut the turbine down to replace the cooler.
VARTECH ISC was added and over one hour, the main oil header temperature dropped around 10 degrees, from too high to normal. The product had an immediate effect on the operating conditions of the oil cooler. In comparison, when the previous dispersant/ detergent product was used, it took two days to see a temperature drop.
That product was also blocking the filters in the system frequently with varnish debris. VARTECH ISC had no such filter plugging effect over the two-day test period. Subsequent testing continued, it revealed that VARTECH ISC outperformed many other commonly used cleaners in cleaning efficiency, effectiveness, and system compatibility without drastically affecting water separability and oxidation stability. This compatibility also reduces the performance impact for the fresh oil when flushing is unfeasible, and it does not need to be used in combination with a varnish filtration system. It is not recommended not to leave any varnish cleaner in a system indefinitely. Simply add VARTECH ISC before a scheduled oil change, and the removed varnish debris will come out with the old oil.